When Accuracy Matters: The Real Cost of Outdated Obsolete Life Cycle Codes
A contractor browses a distributor’s website, selecting crucial items for an upcoming project. The order processes smoothly, but soon there’s a hiccup: one essential item is discontinued. Its life cycle status was erroneously left as “active” when it should have been marked “obsolete.” As the distributor scrambles to offer a substitution, the contractor—pressed for time and frustrated—cancels the order.
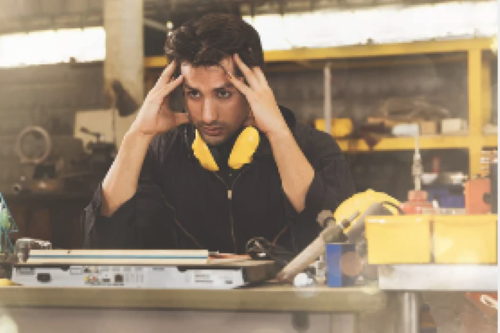
Real-World Challenges
1. Impacting customer buying experiences
This scenario isn’t just a minor irritation; it’s a vivid illustration of how outdated life cycle codes can prevent sales, erode trust, and directly impact the bottom line for both distributors and manufacturers.
According to Nick Becker, data analyst at Standard Electric Supply, when obsolete life cycle codes are inaccurate, it disrupts the entire order process and creates a disappointing buying experience.
“At Standard Electric Supply, the customer’s experience is what’s really important. Our goal is to provide the best and latest products to customers,” Becker explains. “When we’re notified about products’ obsolescence, we can avoid these situations where we don’t have the product. This helps us ensure that the customer has the newest product and a smooth buying experience.”
2. Costly dead stock
When distributors aren’t notified that a product is becoming obsolete, it can lead to dead stock: inventory that becomes unsellable. This can lead to financial losses and waste, which is bad for profits and the environment. Excess inventory of an obsolete product causes distributors like Standard Electric to “backtrack, figure out what happened, make a case for returning the product, sell it elsewhere, or scrap it,” said Becker.
3. Confusion due to premature obsolescence
Another challenge is premature obsolescence, which occurs when products are mistakenly marked as obsolete before their actual end-of-life.
“When products are marked obsolete too early, the product is active and still available for sale months later. This causes confusion, inventory challenges, and hardship internally for salespeople who are trying to get the current product into the customer’s hands,” Becker explains.
Hear more from Nick Becker on IDEA’s YouTube Channel.
Provide accurate product life cycle with status codes
IDEA Connector’s comprehensive lifecycle management tools track a product’s journey from introduction to discontinuation. The Introductory status (I) prepares products for market entry, while Active (A) status indicates items currently available for sale. As products reach stability in their lifecycle, they are marked as Mature (M), signaling established presence in the market. Planned Obsolescence (P) marks products slated for phase-out, Obsolete (O) indicates products no longer available for order, and Deleted (D) signifies legacy information on items that are no longer manufactured.
Understanding Obsolete Codes and Their Importance
End-of-life codes enable manufacturers to communicate product phase-out plans effectively to distributors, ensuring that both parties can manage inventory levels appropriately and prepare for products that will be discontinued or replaced. These codes are crucial for distributors to manage their stock levels effectively and avoid accumulating unsellable inventory. It also ensures that sales teams focus on viable products.
IDEA Connector End-of-Life Product Codes (as used by manufacturers)
- Item Status (P) – Planned Obsolescence
Item is planned to be phased out. This indicates that an item will soon be replaced or discontinued, with limited quantities available. - Item Status (O) – Obsolete
Item is no longer available for order and has been phased out by manufacturers. Best practice for manufacturers: identify the replacement or substitute products on the obsolete product record so distributors can transition customers to the new replacement product. - Item Status (D) – Delete
Item is retained in the IDEA Connector database until it is removed. This legacy information enables distributors to find replacements while designating that that an item is no longer manufactured due to various reasons like end of life, SKU reduction, low activity, or errors in listing.
Best practices
Nick Becker emphasizes the need for better communication and consistency in obsolete life cycle updates.
“From a database management perspective, we like to keep our data clean and lean. Suppliers are inconsistent in how they use life cycle codes. We prefer that suppliers update the codes in IDEA Connector, but some email or send them to other people in the company, and it creates a fragmented process,” said Becker.
To improve, Nick suggests more suppliers populate and update the obsolete codes in IDEA Connector.
“We’d like to see more suppliers use IDEA Connector and provide notifications about obsolete status changes to us through its messaging system. Most of the IDEA Connector data is really good, but manufacturers could improve how they handle obsolete codes. Consistent and accurate use of obsolete codes would help distributors to better manage inventory and enable us to serve our customers better,” he said.
Another best practice for manufacturers is to retain product data in IDEA Connector for at least two years after a product is designated as obsolete. This ensures that distributors have access to essential information to effectively manage and sell their remaining stock. When manufacturers remove SKUs and related product data from IDEA Connector prematurely, it can create significant challenges for distributors.
Stay tuned for our next article in this series, where we will delve into the best practices for product introduction codes. Read our previous overview article on Product Life Cycle Codes.
IDEA product obsolescence tools
- IDEA Connector Product Life Cycle Chart
- Item Status Definitions & Usage in IDEA Connector
- Request Product Life Cycle Updates through the Data Quality Hub
- Using IDEA Connector Broadcast Emails for notifications
Questions? Reach out to IDEA Customer Success.